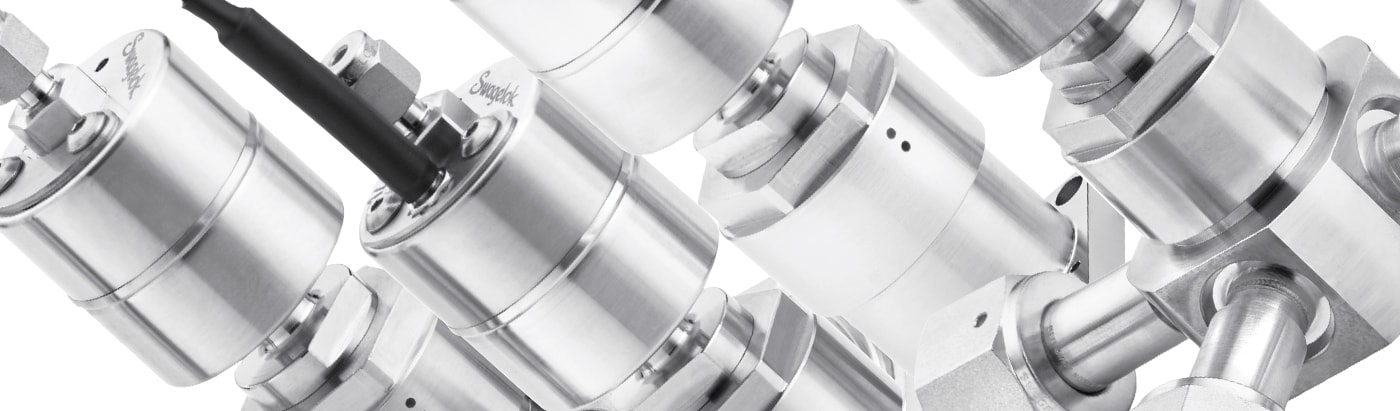
高流量世伟洛克® ALD20 超高纯阀门具有世伟洛克® ALD 阀门应有的可靠性和性能,同时还具有以前无法实现的温度稳定性和流量可能性。它使制造商能够尝试不同的工艺和低蒸汽压化学成分,以便在不显著改变工艺的情况下实现开发先进技术所需的均匀气体沉积。
世伟洛克 ALD20 阀门可以:
- 在与现有 ALD 阀相同的占用空间 (1.5 in.) 中提供 1.2 Cv 的流量,从而在无需重新装备的情况下提高性能
- 以稍大 (1.75 in.) 的标准变体提供更大的 1.7 Cv—流量,这也是目前超高循环寿命、超高纯阀门可提供的最高流量
- 可浸入温度从 50°F (10°C) 到 392°F (200°C) 的气箱中,从而无需在加热期间隔离执行机构并提高沉积一致性
- 采用 316L VIM-VAR 不锈钢或 22 合金阀体材料选项,增强了耐腐蚀性能
- 采用 5 μin. Ra 表面处理的高度抛光型波纹管,可在超高循环寿命期间支持清洁操作,从而确保工艺完整性
- 实现高速 (<10ms) 的可重复性驱动,以实现精确而一致的流量,从而满足计量要求
还可提供定制的流量系数。
ALD20 阀门规格
工作压力 | 真空至 20 psig (1.4 bar) |
爆破压力 | >3200 psig (220 bar) |
执行压力 | 70 至 90 psig(4.9 至 6.2 bar) |
温度 | 50° 至 392°F(10° 至 200°C) |
流量系数 (Cv) | 1.2 (MSM) 或 1.7(直通型) |
阀体材料 | 316L VIM-VAR 或合金 22 |
波纹管材料 | 合金 22(5 μin. Ra 表面处理) |
端接 | 类型(尺寸):内螺纹 VCR® 接头 (1/2 in.),可旋转外螺纹 VCR 接头 (1/2 in.),卡套管对焊,长 0.50 in. (1/2 in. x 0.049 in.),模块化表面安装高流量 C 型密封 (1.5 in.) |
在选择 ALD 阀门时需要帮助吗?
ALD20 系列阀门目录
查找详细的产品信息,包括结构材料、额定压力和温度、选购件及配件。
ALD 3, 6, and 7 Diaphragm Valves and ALD20 Bellows: Ultrahigh cycle life, high-speed actuation; Up to 392°F (200°C) w thermal actuators; Electronic actuator position-sensing; ultrahigh-purity applications; High flow capacity, PFA seat, Normally closed pneumatic actuation, Alloy 22 available
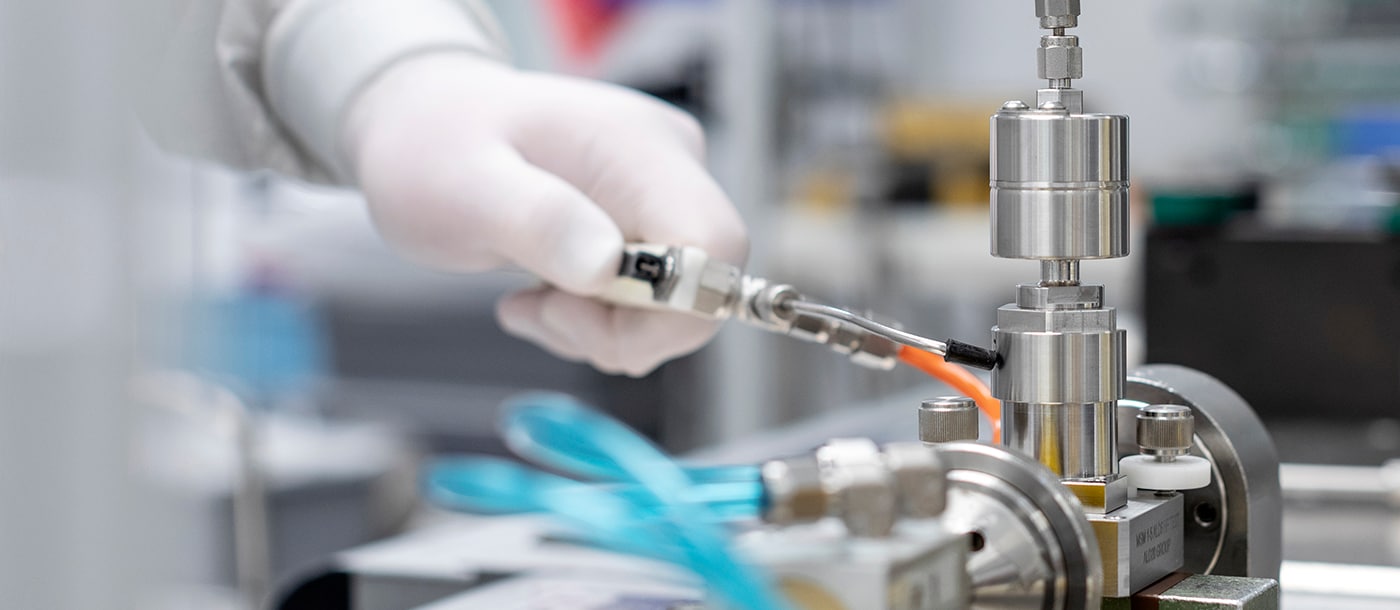
世伟洛克为您精心准备的产品、服务和解决方案
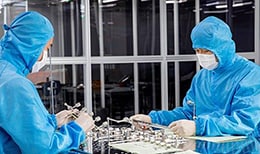
利用优化的合金提高半导体制造良率
了解半导体制造商如何通过为关键流体系统组件选择合适的金属材料,提高端到端制造良率并提高长期盈利能力。
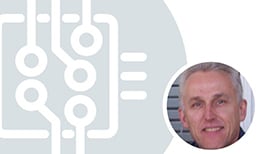
问答:半导体制造的过去、现在与未来
了解半导体OEM设备商、微芯片制造商与流体系统解决方案提供商之间的协作如何使半导体市场在数十年来能够满足摩尔定律的要求以及未来的发展方向。
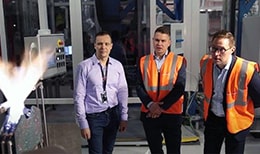
Fiber Optics Equipment Manufacturer Increases Efficiency with Customized Solutions
Since the 1980s, Rosendahl Nextrom has depended on Swagelok to move its business forward. Learn more about the solutions that allowed the company to outpace its competitors and remain an industry leader.
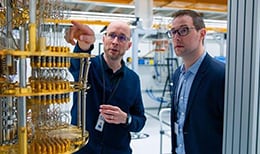
Reliable Fluid System Solutions for the Scientific Frontier
Learn why Finnish dilution refrigerator manufacturer Bluefors trusts Swagelok for fluid system components and solutions that help enable quantum computing, experimental physics, and more.